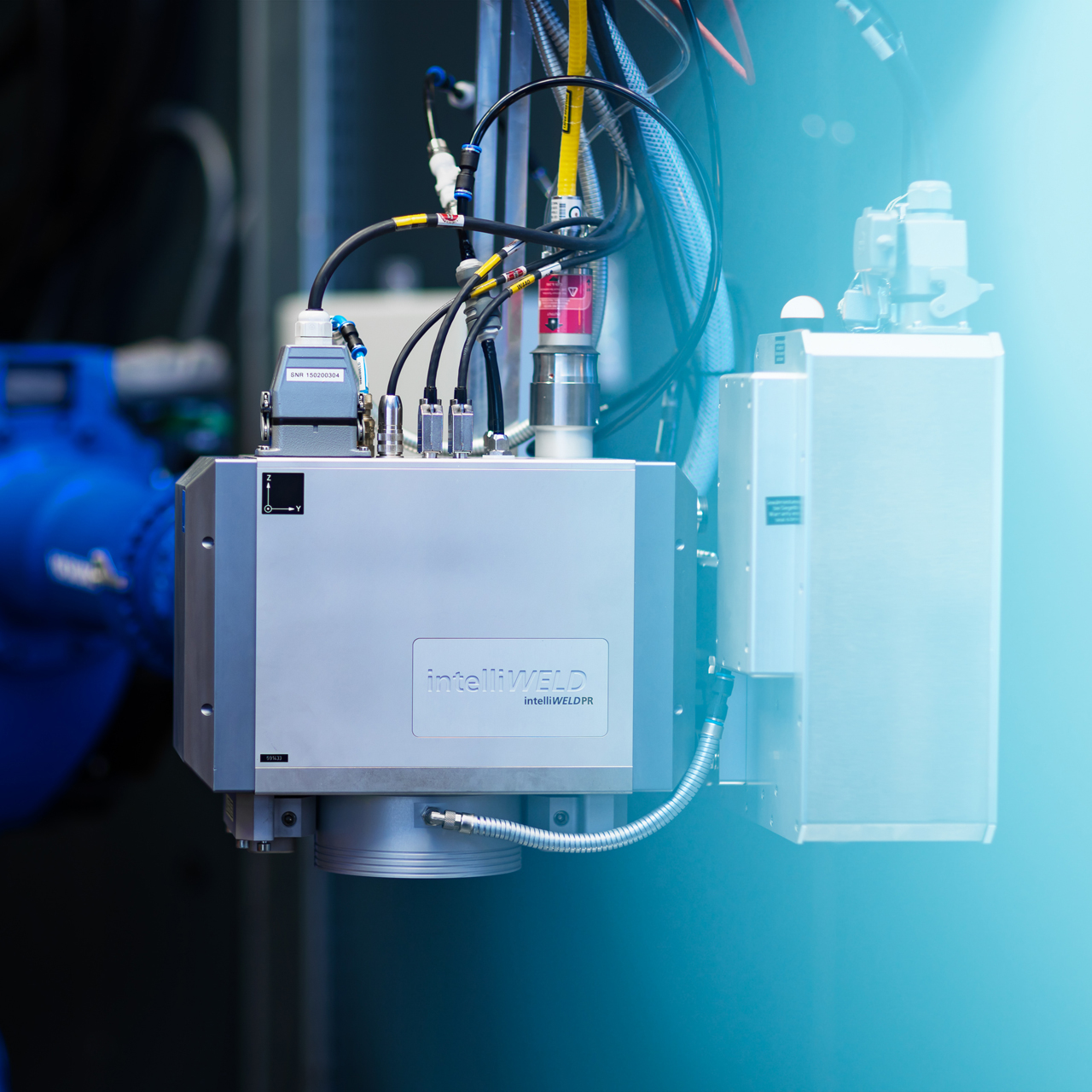
Laser Welding with OCT
Laser welding benefits greatly from integrated process monitoring technology, which makes it possible to quantify and qualify the joining process in many ways before and after processing.
Blackbird is the pioneer and the technology leader for the application of the optical coherence tomography (OCT), the universal sensor technology for the process monitoring of scanner based laser welding processes. OCT permits the recording of a variety of geometric features in the joining zone of a welding process and its adjacent environment.
One of the largest benefits of the OCT measuring process is that process lamps do not have an influence on the acquired signal quality. This also permits the measurement of the keyhole depth during the process.
OCT Application Areas
- Pre-Process: Recording of the component position for the correction of the seam position
- In-Process: Measuring the depth of the steam capillary, the keyhole
- Post-Process: Recording of the geometric characteristic of the welded seam
User friendliness and the best possible signal quality while utilizing the maximum process dynamics were the main focus from the start of the product development. For this purpose, Blackbird newly developed - jointly with SCANLAB - all required mechanical, optical and electrical components to be able to offer the best possible system technology for the remote laser welding in connection with OCT.
The specifically developed OCT scanner (Blackbird xHAWK) permits the OCT beam positioning even under fast feed rates, beam oscillation frequencies up to 1000 Hz and the unrestricted utilization of the scan volume of the 2D or 3D scan system used for laser welding.
Benefits of a Configuration with OCT Scanner
- Large OCT scan field
- High dynamics and accuracy of an OCT scanner
- Precise synchronization of main scanner, OCT scanner and OCT sensor system
- On-the-fly machining
- One software solution for the entire configuration of the welding process incl. OCT
- Spatial resolution of 50 µm or better
- Compatible with beam oscillation of up to 1000 Hz
- Successfully tested for welding speeds up to 10 m/min
Typical System Configuration
- intelliWELD or intelliSCAN (on request) scan system
- OCT scanner (Blackbird xHAWK)
- ScanControlUnit (SCU)