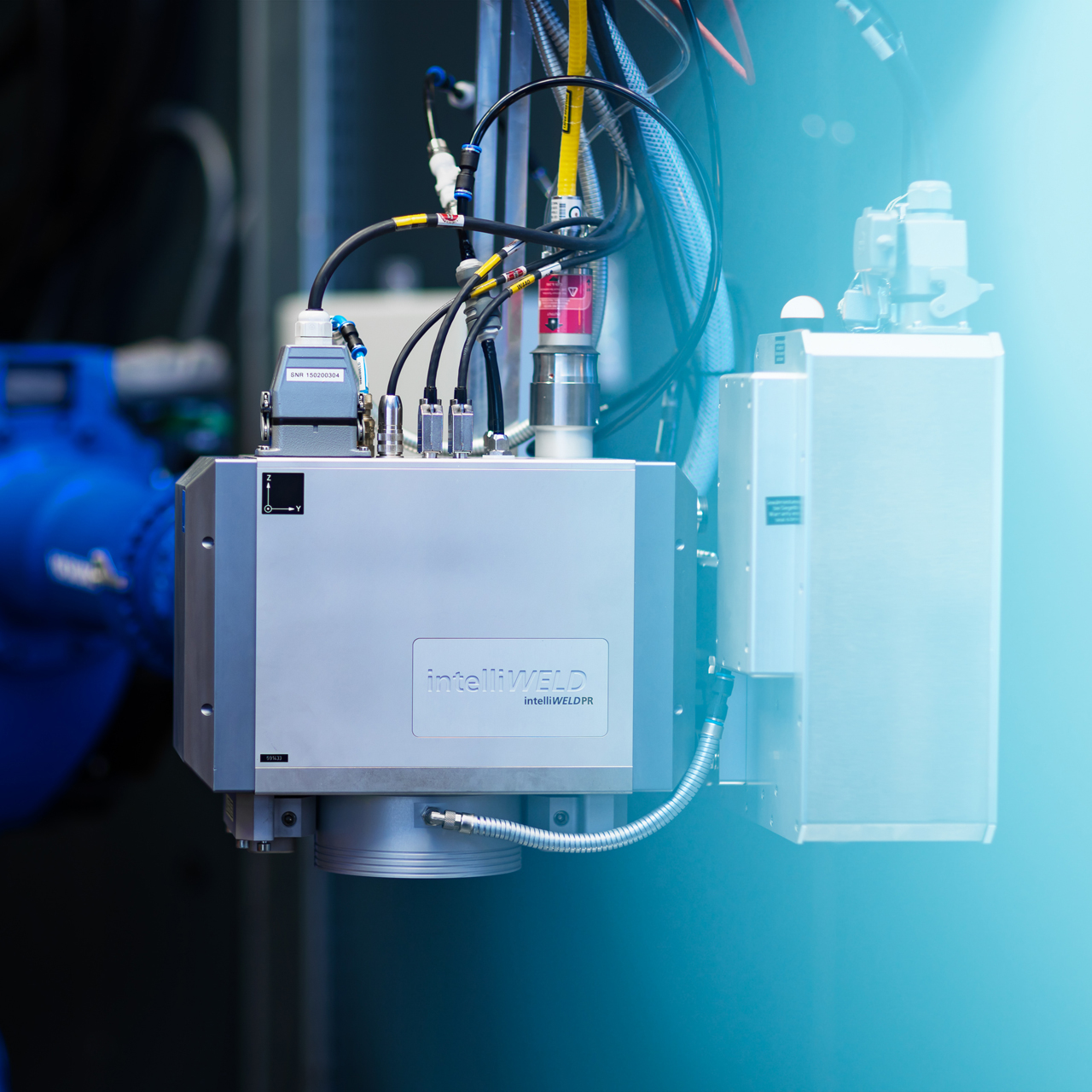
Welding Seam Tracking with OCT
Depending on the requirements, the laser beam must be focused on the component with an accuracy of a few tenth of a millimeter, in some cases with an accuracy of 100 µm. This represents a significant challenge for the user especially in case of robot guided applications or large components.
The OCT (optical coherence tomography) based seam tracking makes it possible to guide the laser beam continuously with precision on the component. OCT guarantees this also for larger deviations that were caused by warpage, form or position tolerances or deviations of the guide tool. The component geometry and position is recorded and the position of the laser beam is adjusted for a precise seam tracking in a few milliseconds immediately before the joining process (Pre-Process).
The OCT measuring process also permits the recording of the distance between upper and bottom plate and to react to variations of the gap between the components. In case of a widening gap, the laser power can, for example, be increased or the position of the processing beam can be moved on the upper plate. A combination with beam oscillation is also possible: If a gap opens in this case, then the amplitude of the oscillation can be increased to increase the volume of the molten material and to bridge the gap.
The OCT seam tracking can be used without restrictions for static and on-the-fly applications. 3D scan fields with seams on different or varying levels can be implemented by using seam tracking.
Typical Application Areas
Welding seam tracking with OCT provides huge benefits when remote laser welding is used for
- Vehicle doors (fillet welds or lap welds with reference edge)
- Car seats
- Battery trays
- Body-in-white (e.g. A/B columns, cross girders)
then the welding seam tracking with OCT provides huge benefits.